Today’s supply chains need to be prepared for the unpredictable, including disasters, climate change and geopolitical risks. Fujitsu’s Supply Chain Risk Visualization, a Uvance solution, provides customers with a single pane of glass view of the risks a supply chain must manage.
Powered by Fujitsu’s procurement expertise, the system integrates all types of information about production facilities and components, enabling companies to respond more quickly in the event of a disaster.
Fujitsu implemented the service internally in 2025 and has since enhanced its resilience.
Challenges
- Increasingly severe and frequent natural disasters
- Time consuming work (3 weeks to 1 month) to assess supply chain damage
- Difficulty in capturing full damage picture (e.g., primary, secondary, and tertiary suppliers)
- Delays in obtaining information on disasters abroad
Solutions
- Implemented “Supply Chain Risk Visualization” service
- Map showing location of supplier plants and disaster information to help customers assess impact
- Automated disaster notification system for registered suppliers
Outcomes
- Significant reduction in initial response time
- Visualized potential risks at manufacturing sites to help a client develop contingency plans
- Easier to identify overseas disasters through SNS integrated feature
“Thanks to the system, it has become much easier to respond to disasters, including those that have occurred overseas. The maps have also helped us with faster damage assessments in procurement.”
Seiji Tanaka, Senior Director, System Platform Business Group Network Products SCM Div., Fujitsu
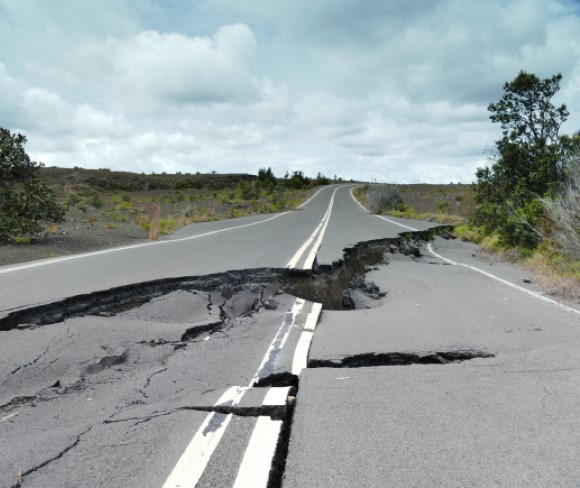
300
The number of primary suppliers involved in the production of a networking product
- Industry: Manufacturer
- Location: Japan
- People: 124,000
- Customer's website
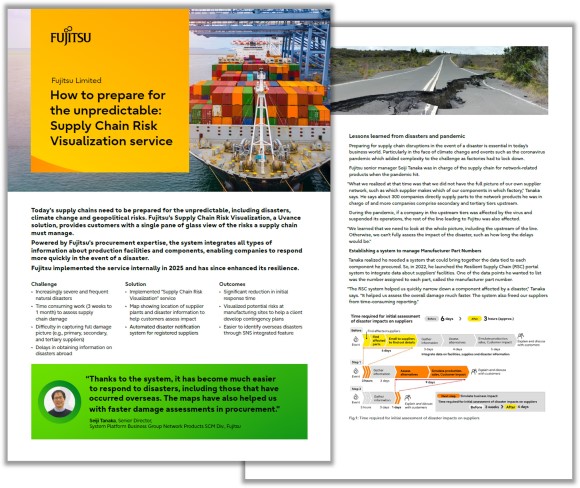
About the customer
Our Purpose is to make the world more sustainable by building trust in society through innovation. With Fujitsu Uvance, we will help customers build a resilient supply chain and contribute to a Net Positive world.
Preparing for supply chain disruptions in the event of a disaster is essential in today’s business world. Particularly in the face of climate change and events such as the coronavirus pandemic which added complexity to the challenge as factories had to lock down.
Fujitsu senior manager Seiji Tanaka was in charge of the supply chain for network-related products when the pandemic hit.
“What we realized at that time was that we did not have the full picture of our own supplier network, such as which supplier makes which of our components in which factory,” Tanaka says. He says about 300 companies directly supply parts to the network products he was in charge of and more companies comprise secondary and tertiary tiers upstream.
During the pandemic, if a company in the upstream tiers was affected by the virus and suspended its operations, the rest of the line leading to Fujitsu was also affected.
“We learned that we need to look at the whole picture, including the upstream of the line. Otherwise, we can’t fully assess the impact of the disaster, such as how long the delays would be.”
Establishing a system to manage Manufacturer Part Numbers
Tanaka realized he needed a system that could bring together the data tied to each component he procured. So, in 2022, he launched the Resilient Supply Chain (RSC) portal system to integrate data about suppliers’ facilities. One of the data points he wanted to list was the number assigned to each part, called the manufacturer part number.
“The RSC system helped us quickly narrow down a component affected by a disaster,” Tanaka says. “It helped us assess the overall damage much faster. The system also freed our suppliers from time-consuming reporting.”
“Supply Chain Risk Visualization”, a powerful map displays hidden risks
“The Supply Chain Risk Visualization Service (SCRV)”, developed by Fujitsu, was implemented in January 2025 as an upgrade for the RSC system.
Like its predecessor, SCRV integrates data on suppliers’ manufacturing locations and the items produced.
One of its unique features is the maps. They show the locations of manufacturing sites along with hazard information and weather warnings in a single view.
Tanaka says the map helps him understand the situation in case of a disaster. “For example, let’s say there was a big earthquake. I would check the map to make sure that suppliers’ plants at the epicenter and those nearby were not affected. I think it allows us to expand the scope of our response.”
Another notable feature of SCRV is that it automatically sends alert e-mails to registered suppliers when disaster information is released. This includes overseas disasters that are confirmed via SNS.
Tanaka says that response to overseas emergencies has tended to lag behind due to a lack of information officially released domestically.
“The first day or two of the initial phase is crucial in an emergency. We believe that our customers will also be able to respond much more quickly once the system is up and running.”
Fujitsu will continue to be committed to contributing to the supply chain risk management of its global customers through the SCRV service.
Related Customer stories
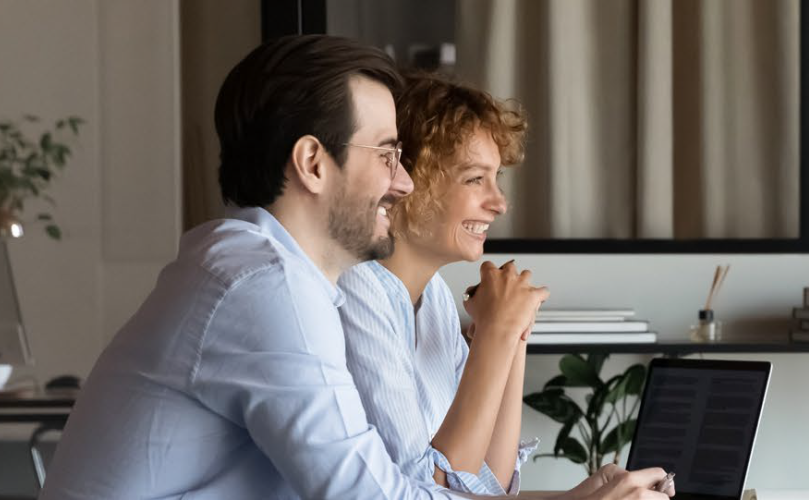
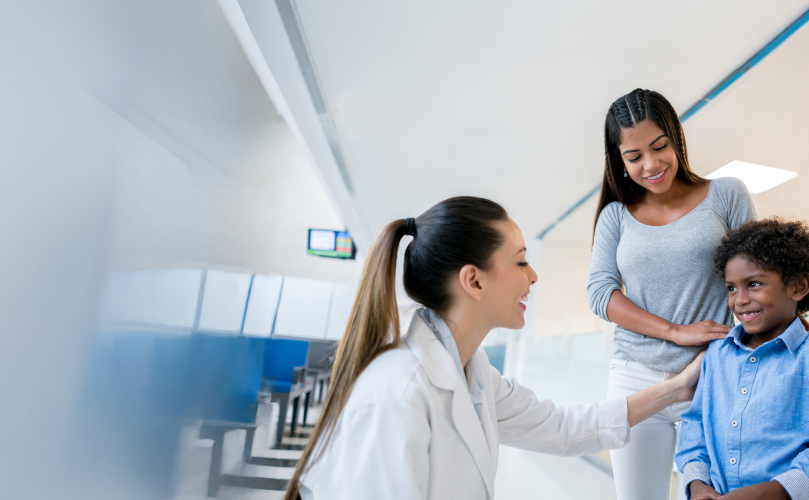
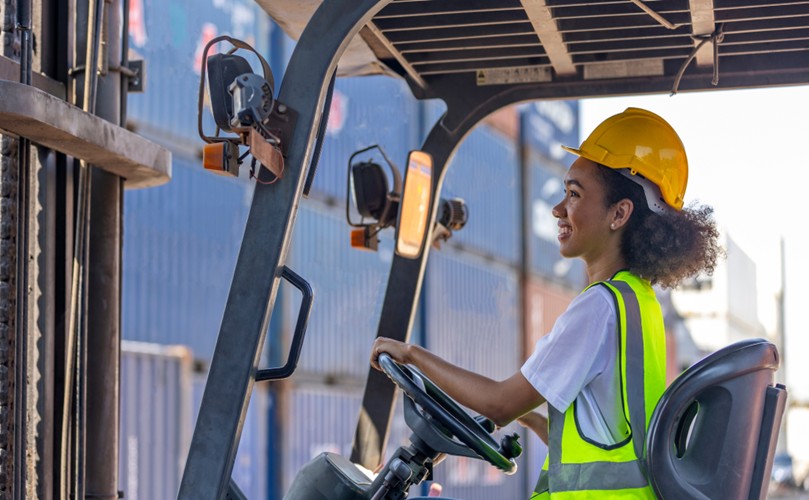
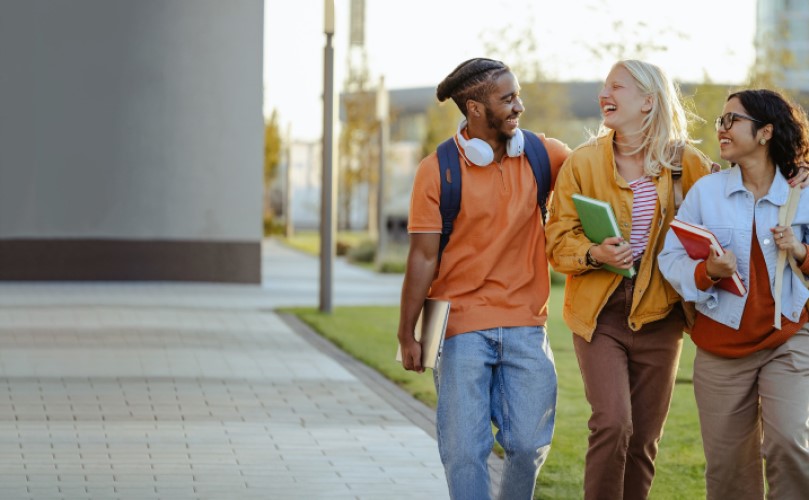